Boeing and its airline and defense customers are applying besides testing automation and digital innovation throughout the product lifecycle.
As part of design automation, Boeing utilises digital twin technology to optimise design and development processes.
“Digital twins are precise digital replicas of physical assets or products that simulate their behavior in real-time. Using digital twins, Boeing improves design efficiency and reduces manual processes. This technology allows engineers to extensively test aircraft performance and systems, resulting in improved first-pass quality, maintenance, and sustainability over the entire life cycle of the aircraft,” Boeing said in an interview with Gulf Times.
The Boeing T-7A Red Hawk advanced trainer is widely considered the first digital pathfinder jet, embracing advanced manufacturing techniques to improve quality and enhance performance.
Using model-based systems engineering and 3D design tools, the T-7A represents an aircraft with a 75% increase in first-pass quality and an 80% reduction in assembly hours. The aircraft moved from firm concept design to first flight in just 36 months.
Automation in manufacturing: Boeing's manufacturing facilities are increasingly utilising robotics.
Collaborative robots, or "cobots," are working alongside human colleagues in Boeing Aerostructures Australia (BAA) in Melbourne. These autonomous cobots use sensors to prevent collisions and independently select tools in dynamic work environments, streamlining the production process and ensuring safety and first-pass quality.
Boeing’s South Carolina facility in the US utilises a quadbot, comprised of four robots, for drilling approximately 3,000 holes in the aftbody of the 787 Dreamliner.
The quadbot then inspects the holes, applies sealant, and installs fasteners, exemplifying two decades of Boeing's innovation in automated drilling. Additionally, Boeing uses automated fiber placement machines for laying carbon fiber tape on the aftbody of the 787 Dreamliner, optimizing production efficiency.
On the defense platforms, a 4.5-meter-tall robot is busy drilling holes into a Boeing F-15 wing at the Boeing’s St. Louis factory in the US. It receives precise guidance thanks to a Boeing-developed software application.
In the space domain, Boeing’s research and development work helps automate the thermoplastic composites welding process. These innovations ensure that there are safe processes in place that reduce touch labor and increase safety for the next generation of crewed and uncrewed spacecraft.
Operations: Boeing’s digital solutions provide the software and services to improve performance and reliability across all phases of flight for all types of aircraft, across commercial and military, business, and general aviation.
From advanced flight deck and navigation solutions to flight operations and maintenance, Boeing helps customers operate more efficiently, reduce fuel consumption and carbon emissions, optimize flight and crew planning and scheduling, and minimize the impact of disruptions on their operations.
Boeing couples design and production with a digital approach to maintenance, sustainment and training systems to better support airline and military customers. From virtual training to augmented reality maintenance guides to predictive maintenance tools, the digital focus underpins all Boeing’s solutions.
As an example, the company is developing the Autonomous Aircraft Inspection (AAI) system that employs drones to perform routine inspections on aircraft for issues such as corrosion and missing rivets. This automation offers increased accuracy and efficiency.
In addition to customers, Boeing collaborates with government and academic institutions to drive technological advancements and inspire the next generation of aerospace scientists and engineers in the Middle East and beyond.
Initiatives include working with Qatar University College of Engineering. Boeing supports the university’s students’ projects to design and test uncrewed aerial vehicles (UAVs) and vision bots capable of complex tasks.
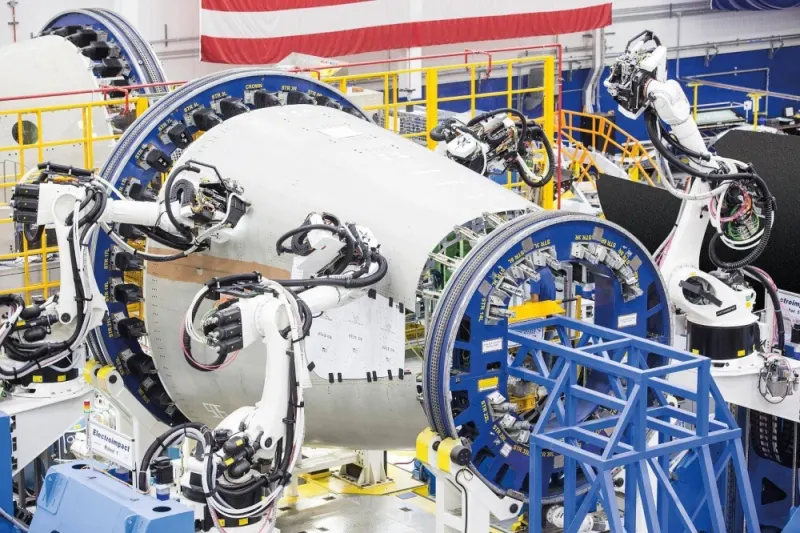
Boeing’s South Carolina facility in the US utilises a quadbot, comprised of four robots, for drilling approximately 3,000 holes in the aftbody of the 787 Dreamliner aircraft.