College of the North Atlantic-Qatar (CNA-Q)’s new refinery simulator software gives the institute’s graduates a distinct advantage before they enter the oil and gas workforce. The advanced technology used as part of the virtual refinery simulator training is the first of its kind in the GCC.
“Along with our state-of-the-art scale version of a modern processing plant, this 3D virtual reality software model provides our students with methodology in all aspects of a modern refinery, both for control panel and field operator training. Operations can be carried out in real time, allowing students to quickly and correctly solve operating problems,” said Jim Bathgate, associate dean of industrial trades at CNA-Q.
CNA-Q has several process control simulators working in tandem with the Oil and Gas Training Centre - also the first of its type in the region. The facility is dedicated primarily to the Technician Preparatory Program (TPP). The simulator training for outside operators, console operators and supervisors is essential to providing realistic training for the entire operations team in a refinery.
Emphasis is laid on developing a variety of competencies, including practical, problem-solving and technical communication skills, as well as the ability to work as part of a team to deliver training at the highest level. The college also uses the Student Performance Analysis (SPA) package - a comprehensive set of analysis and trading tools.
“Our approach is to combine our operator training simulator with a virtual reality-based outside operator station,” said Barney Hayden, lead process operations instructor at CNA-Q. “This allows all students to participate and learn with real-time practice. It gives them the freedom to practice repeatedly using a combination of events so that they can quickly learn how to solve real operating problems.”
The instructor can use the software to see the progress made by a student with each action and reaction, getting an accurate indication of one’s comprehension of practices.
Yousuf al-Sada is in his final semester of the TPP training, after which he will become a process operator at RasGas in Doha. He is enjoying the training and, in particular, the virtual simulator.
“We learn to control hazards in a plant and focus on environmental safety. I finish my training in April and look forward to starting work,” said Yousuf. “I feel comfortable working in the control room and outside.”
Another benefit of the virtual reality simulator is that it allows teams of operators to work together - one outside and the other inside. With traditional simulators, the only “audience” is the console operator, disconnected from the rest of the team.
Additionally, this approach creates a lively interactive experience for trainees and provides additional support for all individuals and teams simultaneously. “Controlling a chemical processing plant is highly team dependent. Without this software programme, students learn independently and do not develop communications skills that are required in a real-world job,” said Hayden. “With this technology, our students are able to learn efficiently and in a team-based environment while we monitor them in real time.”
On the job site, lack of communication and poor team performance can lead to mishaps, causing injuries and damage to equipment.
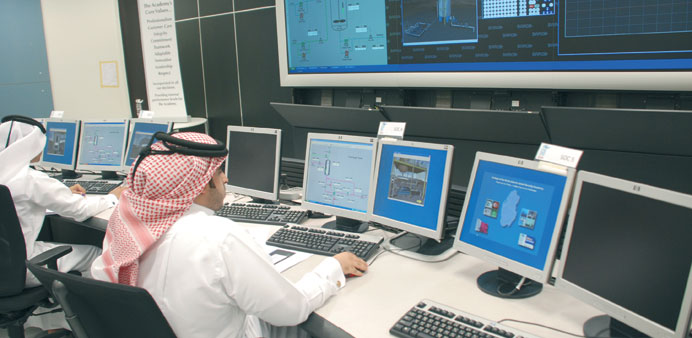
Students undergoing virtual refinery simulator training.